高熔体流动速率PP的开发
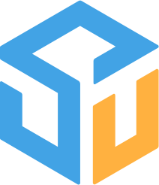
摘 要:综述了国内外典型高熔体流动速率、薄壁注塑成型聚丙烯(PP)的反应器特点。剖析了典型薄壁注塑成型用PP的性能,发现Unipol工艺单反应器在生产薄壁注塑成型用PP时,存在H2需求量高、高H2浓度条件下反应器控制困难、挤出造粒困难的问题。详细分析了引起这些问题的原因,并给出了相应解决方案:可通过升级现有邻苯二甲酸酯类催化剂体系,增加催化剂氢调敏感性;缓慢建立H2组分,适当提高丙烯分压,保证床层温度及露点温差;降低过滤网目数并相应调整造粒机的各工艺,以避免缠刀及连锁停车。
关键词:聚丙烯 薄壁注塑 高熔体流动速率开发
聚丙烯(PP)杰出的力学性能、耐热性能以及电绝缘性能和低廉的价格、优异的加工性能,使其被广泛用于汽车、航空、电子、日用品以及医疗等行业。随着产品设计理念向“轻、薄、短、小”方面发展,加之人们对食品安全和环境保护的日益关注,采用无毒无害、微生物可降解、可注塑成型薄壁制品的PP(简称薄壁注塑PP)作为食品包装、储存、加工材料已成为一种新的发展趋势。
我国薄壁注塑PP的开发起步较晚,2014年以前,我国华南、华东等发达地区薄壁注塑PP几乎完全被韩国、马来西亚等国家的进口PP占据。随着近两年网上外卖平台的风靡,全国范围内对一次性塑料餐盒的需求呈爆发式增长,国内各大企业开始致力于高熔体流动速率(MFR)薄壁注塑PP的开发。该PP在生产制品的过程中可采用一模多腔注射成型,替代以往采用的挤出片材再热成型的两次成型工艺技术,降低生产成本、缩短加工成型周期。
从2016年至今,国内先后有4家企业开发出薄壁注塑PP,国内共有约10家企业具备生产条件,且PP产品基本处于供不应求状态。据统计,2017年,全国外卖行业共消耗一次性餐盒280亿个,大约需要一次性餐盒850 kt,其中,PP餐盒用量占700 kt,薄壁注塑PP需求量约630 kt。就2017年统计,国内年产量约450 kt,仍有近180 kt的市场缺口,部分仍依靠进口。
国外对薄壁注塑PP的研究较为成熟,目前在沿海一带仍然具有较大的市场占有率,主要流通的PP牌号有韩国三星集团道达尔石化有限公司的HI828、马来西亚大腾石化有限公司的HP740P及韩国大林集团实业有限公司的PM830。
随着国内薄壁注塑PP产品的不断本土化,进口产品势必受到打压,但就目前看,国内产品质量参差不齐,性能有待改进。随着外卖平台的不断推广,一次性餐具行业增长势头不减,未来薄壁注塑PP的需求量将稳中有增,市场前景较为广阔,国内产品完全替代进口产品的道路依旧任重道远。
01 薄壁注塑关键性能
收集了3种国内市场较认可的薄壁注塑PP,从表1可以看出:
1)薄壁注塑PP具有较高MFR,均达60.0~70.0 g/10 min。薄壁注塑PP主要用于生产一次性餐盒、杯子,需要快速注塑成型。目前,下游主流客户使用的注塑机均为“一出四”的模具,并正在向更高效率的“一出六”及“一出八”方向发展,因此要求PP具有较高的MFR,以保证较好的流动性。MFR低,不仅需要更高加工温度,还会造成制品外观缺陷。
2)薄壁注塑PP具有较高弯曲模量,大于1500 MPa。目前,一次性餐具主要用于餐饮外卖打包领域,所接触的食品多涉及高温环境,因此需要保证制品具有较好的弯曲模量,一方面能避免制品出现翘曲现象,影响外观及使用性能;另一方面能保证制品具有较好的耐蠕变性及耐热性,满足高温食品的存放需求。
3)适当的冲击强度,客户要求最佳悬臂梁缺口冲击强度为2.00~3.50 kJ/m2。一次性餐盒在冬季或寒冷地区运输及终端使用过程中,不仅要求制品具有较好的耐翘曲性能,还应保证制品具有适当的韧性。因此,一次性餐盒生产企业均通过传统的“跌落实验”检测制品韧性,部分下游加工企业为了满足市场需求,选择在加工过程中掺混5%~10%的线型低密度聚乙烯以增加制品韧性。从试样A的性能可以看出,部分生产企业通过在PP中引入质量分数为1.0%的乙烯,生产无规共聚PP,从而在确保弯曲模量满足需求的前提下明显提高冲击强度。
4)较低的黄色指数,即需低于-2.0。一次性餐盒多数为透明制品,随着人们审美需求的不断提高,要求制品具有较好的透明性,因此,生产企业一般在PP中添加少量成核剂,增加PP刚性的同时具有一定的增透性。从对试样A的剖析可知,部分企业直接在PP中添加增透剂,得到“蓝相”高结晶PP,最终制品呈现发蓝的现象。
02 国内薄壁注塑PP生产工艺分析
国内具备高MFR的薄壁注塑PP生产能力的企业约10家,目前市场认可度较高的生产企业及相应的生产工艺见表2。
2.1 三井油化的Hypol本体-气相组合工艺
国内使用三井油化Hypol本体-气相组合工艺的PP装置较多,目前采用该工艺生产的、市场认可度较高的薄壁注塑PP是兰州石化生产的H9018或H9018H,聚合工艺反应器组合见图1。
Hypol本体-气相组合工艺采用3个反应器串联,2个液相搅拌釜反应器和1个气相反应器。通过加H2调节MFR的方法(简称氢调法)生产薄壁注塑PP,需要保证H2与反应物分子链的充分接触,因此需同时向3个反应器添加H2。3个反应器分别控制MFR在30.0~35.0,35.0~40.0,45.0~60.0 g/10 min,通过较长的停留时间逐步达到最终PP产品性能要求。
该工艺虽然能较好地控制反应平稳性,但由于液相丙烯与H2的相容性较差,加H2反应主要在气相与液相界面上进行,存在较难控制H2浓度的缺点,只能通过加大循环气的鼓泡作用及增大H2浓度来生产薄壁注塑PP。
2.2 格雷斯的Unipol气相工艺
目前,国内在运行的Unipol工艺装置约14套,其中,采用该工艺,并且具备薄壁注塑PP生产能力的是山东联泓,牌号为PPR-M600N,工艺反应器示意见图2。
Unipol气相工艺PP装置采用1~2个气相流化床反应器,生产均聚PP及无规共聚PP时仅需单个反应器。由于该工艺属于完全气相反应器,H2与气相丙烯相容性较好,可较快达到反应所需组分浓度,因此有利于生产高MFR的PP,过渡料较少。由于H2的加入促使反应活性上升,因此对反应的控制提出了较高的要求。
2.3 巴塞尔的Spheripol本体-气相组合工艺及国产二代环管工艺
巴塞尔的Spheripol本体-气相组合工艺及国产二代环管工艺在生产均聚和无规共聚PP时,其反应器组合情况基本一致,均由一个预聚合反应器与2个环管反应器串联,其工艺反应器示意见图3。
该工艺为液相反应,由于双环管内设有轴流泵,因此反应较为均匀,PP质量稳定性好,可以避免出现局部热点、爆聚等问题;但同样存在H2与液相丙烯相容性差的问题,因此需分区加入H2,增大H2与液相丙烯的接触时间。
03 薄壁注塑PP生产难度及对策
3.1 H2加入量过高
氢调法生产高MFR薄壁注塑PP时,主要依赖H2为链转移剂控制PP相对分子质量。与传统的后系统添加过氧化物降解生产高MFR的PP相比,其H2加入量较大,约0.14~0.40 kg/t。
从生产使用的催化剂来看,目前薄壁注塑PP的生产大多使用第4代齐格勒-纳塔催化剂,该催化剂体系以邻苯二甲酸酯(DIBP)为内给电子体,H2调节MFR的敏感性较差。且该催化剂体系中DIBP为“塑化剂”,对身体健康存在一定影响。鉴于此,已有企业开始使用氢调敏感性更好且不含“塑化剂“的二醚类催化剂来生产和开发薄壁注塑PP。
3.2 高H2浓度条件下聚合工艺的控制
丙烯聚合时,H2对反应有活化作用,高浓度的H2将明显提高反应活性,导致反应剧烈,容易造成反应器内物料结块。这对于气相流化床的Unipol装置而言更明显。针对该操作风险,在转产过程中需缓慢加入H2,重点监控反应器静电及各床层的温度波动,当局部温度过高,达到 75 ℃时,需适当提高丙烯分压,通过添加新鲜丙烯来保证床层温度及露点温差在0~7 ℃。
3.3 挤出造粒系统优化
挤出造粒机平稳运行是生产高MFR PP的又一关键因素。当PP的MFR较高时,由于物料流动速率快,挤出造粒机容易缠刀、停车,且再开车较困难;另外,由于挤出造粒机的筒体和模板温度控制较低,生产时挤出造粒机的过滤网前后压差高,所以易造成联锁停车。针对此问题,可通过更换较低目数的过滤网,并相应调整挤出造粒机的控制温度,挤出造粒机筒体温度控制在230~250℃,切粒的冷却水温度降至45~60 ℃。
04 结语
薄壁注塑PP要求具有较高的MFR和弯曲模量,适当的冲击强度及较低黄色指数。典型薄壁注塑PP的生产工艺中,Hypol工艺、Spheripol工艺均为液相聚合,反应控制较稳,不易出现局部热点,但H2与液相丙烯相容性差,需分区加入H2,延长停留时间;Unipol气相工艺反应控制存在较大难度,但能较快实现H2组分的分散,更有利于生产高MFR的PP。
生产薄壁注塑PP的H2用量较高,可通过优选具有较高氢调敏感性的催化剂体系实现低H2用量。Unipol气相工艺中,较高的H2浓度将明显提高反应活性,易造成反应结块,转产中需缓慢加入H2,重点监控反应器静电及各床层的温度波动,适当提高丙烯分压,保证床层温度及露点温差在0~7 ℃。挤出造粒机易缠刀停车,过滤网前后压差高,易联锁停车,可通过降低过滤网目数并相应调整挤出造粒机的工艺参数。
在环保政策的驱动下,PLA、PBAT、PHA、PCL、PBS等生物降解塑料,在一次性餐具、包装、农业、汽车、医疗、纺织等领域的应用正迎来市场发展新机遇。生物降解塑料的改性材料,以及相关助剂,抗水解剂,增韧剂,成核剂,抗菌剂也会有新一轮的创新。
文章来源网络 如侵删
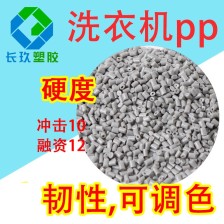
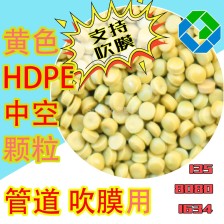
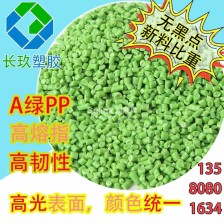