厚壁塑件缩水的原因与解决办法
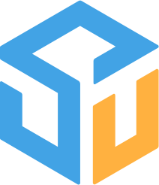
一:厚壁塑件缩水产生原因
塑料件的缩水是成型工艺的常见问题,通常出现在产品的表面上。是因为溶体在冷凝收缩的时候留下的空间得不到补充而出现的。产品冷却凝固时,最外层的先冷却变硬,内部的后冷却(还是软的)。
受到大气压的影响(图1)和材料本身的收缩率的作用下,会向中心区域施压造成下陷。当壁较厚的时候收缩会格外的明显,如果成型时间过短还会造成真空泡,增加冷却时间和填充量收缩程度会明显好转。
二:厚壁塑件缩水解决办法
1、模具设计:
模具设计的收缩不统一,使型芯冷却均匀性不同,肉厚部位比肉薄部位冷却的慢,有热传导的差异,所以肉越厚收缩越大,严重时会出现缩坑。可以将原有(图2)筋位实心的改成非实心的或者对筋位、突出部分变细,增加了水流通过量使该位置冷却充分,增强该位置的冷却效果,缩水程度明显好转。
2、浇口大小:
流道太长或者分流道尺寸浇口太小,溶体流动阻力大,当注入相同计量的溶体,浇口大的注射时间短,反之浇口小的注射时间长;当使用同样的时间,浇口大的填充量会比浇口小的填充量多,封断时间也会延长。
3、材料选择:
材料本身会收缩,不同材料的收缩率不同(表1)。对于尺寸和外观严格的产品应选择分子排列均匀、收缩性小的材料。如表面硬化速度慢的pp料,本身收缩率很大尺寸精度相差也很大,当无法满足设计要求时,可以更换材料或者向原料中兑入防缩剂,增加塑料强度,减小材料收缩率。
4、注塑机原因:
a.射嘴和胶口套有间隙存在溢料,原设有的填充量没有充入模腔。
b.注塑机老化磨损,在监控页面中查看流量阀流量比列均衡和计量单位是否存在大误差。
c.材料中兑入水口料,导致射嘴中存有异物,注射压力和计量达不到设置参数。
5、工艺参数:
a.在工艺中缩水主要所能影响的工艺条件是保压的时间和压力和注射速度,注射速度可以影响溶体流动比,注射速度太慢流道封存就无法填充造成缩水。
b.通常调缩水的办法是增加注射压力、延长保压时间和进胶量等参数,增加过多塑料件产生毛边时,缩水程度还是依旧没有变化,说明只是单单的只从调机参数是无法解决缩水的问题,只能从其他方寻找突破办法。
c.注射速度过慢会使产品填充不实导致收缩,调整工艺参数,采用多级注射,缩水部位适当的增加注射速度,使走在前面的溶体与胶口处产生温差,有利于整个产品的补缩。
6、模具温度:
a.提高模具温度,可以延长凝固点时间,向型腔内注射更多的溶体解决收缩的问题,如图3所示,模温、溶体和凝固点三者的关系。
b.有时模温太低也不利于解决缩水(表面缩水胶口远时),模温太低溶体凝固太快,距离胶口远的位置被中间凝固的溶体堵住补缩路径,适当调整模温,注塑方式采用“慢>慢>快”的方式对缩水位置补缩。
c. 对模具各个部位温度进行检查,是否达到指一致,是否因为水路不通温度过热导致的缩水。
d.在原基础扩充模具内部水路的通过量(ø8的水嘴改成ø10),使模温整体下降。
e.当缩水位置处于浇口附近时,是因为水循环不畅模温过热导致的收缩,排查是否存在堵塞的水路(“死水”)并增加保压时间提高保压压力,缩水程度明显减弱。
7、熔体温度:
a.提高料温,料温过低影响溶体压力传递,使溶体流动不畅,延长凝固点时间增强料的流动性,溶体封断时间变长,可以向型腔内注射更多的溶体解决收缩的问题。
b.料温过高容易产生缩水,适当降低料温10℃-20℃,降低注射速度,能降低分子动向排列顺序收缩量也会减小。
8、储料背压:
适当增加背压,射筒内的熔体均匀压实,排空熔体中空气增加溶胶密度,使分子排列顺序变强,可以改善产品缩水程度。
文章来源:微塑料论坛 如侵删
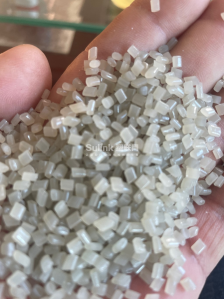
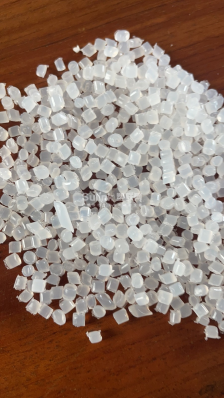
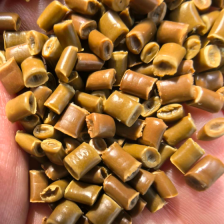