解析:非球面光学零件塑料成型技术
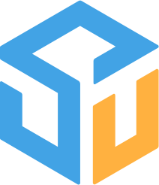
光学塑料成型技术是当前制造塑料非球面光学零件的先进技术,它包括注射成型、铸造成型和压制成型等技术。光学塑料注射成型技术主要用来批量生产直径为100毫米以下的非球面透镜光学零件,也可制造微型透镜阵列。而铸造和压制成型技术主要用于制造直径为100毫米以上的非球面透镜光学零件。
其实在日常生活中,我们也能接触到许多光学塑料,比如照相机的透镜、隐形眼镜等。光学塑料具有良好的可塑成型工艺特性、重量轻、成本低廉等优点,所以在在军事、摄影、医学、工业等领域有着广泛的应用前景。
制造光学塑料一般有两种工艺,包括注射成型、铸造成型和压制成型等技术。其中,注射成型技术主要用来大量生产直径100mm以下的非球面光学零件,也可制造微型透镜阵列;而铸造成型和压制成型则主要用于制造直径为100mm以上的非球面透镜光学零件。
本文主要对注射成型法进行剖析,其中包括日本人发明的高精度塑料光学零件注射成型法——浇口密封成型法。
1、注射成型技术
注射成型法是将经过加热成为流体的定量的光学塑料注射到不锈钢模具中,在加热加压条件下成型,后经冷却固化后,打开模具便可获得所需要的光学塑料零件的一种非球面光学塑料透镜加工技术。该技术的关键环节是模具,由于光学塑料模压成型的工作温度要求较低,所以对模具的要求相对要比对玻璃模压成型用模具的要求低一些。
非球面模具超精密加工相当困难,通常加工都是首先在数控(NC)机床上将模具坯件面磨削成近似非球面,然后用范成精磨法逐步提高非球面的面形精度和表面粗糙度,最后再用抛光法加工成所要求的面形精度和表面粗糙度。然而,由于数控机床的加工精度较低,在模具加工过程中还需对模具反复地进行检测和修改,逐步提高模具的精度,因而使模具的成本费用提高。
为改变这种状况,现在模具加工改用刚性好、分辨率高的计算机数控(CNC)超精密非球面加工机床和非球面均匀抛光机进行。首先用计算机数控超精密非球面加工机床,将模坯加工成面形精度达±0.1微米的非球面,然后用抛光机在保持非球面面形精度不变的条件下均匀地进行轻抛光,大约抛去0.01微米的厚度,使模具表面的粗糙度得到提高。
2、浇口密封成型法
浇口密封成型法,是一种向加热至树脂转化温度以上的金属模具中注射熔融的树脂(注入量应是:冷却结束后打开模具时的树脂的压力刚好等于大气的压力的量) 后迅速将浇口密封,等温度和压力均匀后,在相对容积一定、温度-压力均匀条件下,缓缓冷却至树脂的热变形温度以下后,打开模具取出压型成品的成型方法。
首先,以大约130兆帕的高压将高温熔融的树脂注射到模具中,在高温(T1)。条件下将浇口密封。密封在模具中的树脂压力在均匀化的过程中降至30兆帕,(此时的温度为比树脂转化温度高一些的某一温度T2)。此时只要模具单体能够保持其合模力就不要打开模穴,从树脂注入开始,经过一定的时间后,就可从压型机的合模装置上将单体模具取下。单体模具经过缓缓冷却后才能开模取出压型成品。
该浇口密封成型法由于是树脂注射后用小球进行浇口密封的,因而不需要保压和压缩机构及其工作。所以注射了树脂后的金属模具很容易从成型机上取下来,以金属模具单体脱离成型机身的形式进行长时间的冷却。这不但大大提高了成型机的工作效率,同时也提高了单位时间的生产效率。这种成型法可将一部分功能分配到机外的装置中去完成,改变了过去那种功能只能在成型机装置内进行的做法。
来源:网络,如侵删
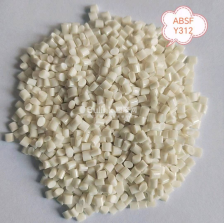
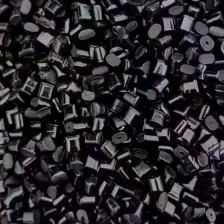
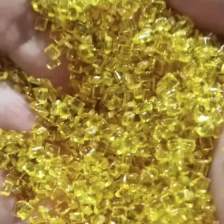